Written by Glenn Eckert | Layfield Geosynthetics
A variety of methods exist to weld geomembranes. The appropriate practice often depends on the consideration of several factors. This technote discusses the standard welding techniques and when they should be applied.
When considering the process of welding two geomembranes together, we need to understand the materials at a molecular level. To weld two compatible materials, their two surfaces must be softened to a certain depth for them to co-mingle and fuse. For most plastics, and therefore most geomembranes, this can be done by one of two methods; thermally or chemically.
When thermally welding plastics together, the two surfaces are softened with heat and then forced together, causing the two materials to mix. Upon cooling, the materials are successfully “welded” together. Chemical welding uses a solvent to soften the two surfaces. When the materials are pressed together and the solvent evaporates, the two materials become “welded” together. While the procedures are entirely different, the outcome is essentially the same. Many other factors must be considered before selecting the appropriate method, such as ambient temperatures, the similarity of the two materials, and the project’s scope.
Hot-Air Welding
Hot-air welders are small, lightweight welders that, just as their name implies, use hot air to soften and join materials together. This welding technique suits all known geomembranes, including PVC, Urethane, HDPE, Polypropylene, and LLDPE. The two overlapping geomembrane layers’ interface is exposed to heated air that softens their surfaces, which are then pressed together to form a strong bond. Hot-air welders are generally used for detail work or to “tack” materials together in the field.
Extrusion Welding
Extrusion welders are larger and heavier welders that use a plastic welding rod forced down a heated barrel by an internal screw. The welding rod is softened, mixed in the heated barrel, and pushed out as a molten plastic bead directly onto the geomembrane liner. A Teflon shoe shapes this molten bead of material over the edge of the overlapped materials. Hot air is blown into the overlap ahead of the molten plastic to soften the material to form a stronger weld. The welding rod used by the extrusion welder must be selected to be compatible with the geomembrane and is often manufactured from the very same resin batch.
This style of welding is primarily restricted to HDPE, Polypropylene, and LLDPE materials, as the likelihood of material degradation in the heated barrel makes this welding technique unsuitable for PVC or Urethane-based geomembranes.
Chemical Welding
Chemical welding only applies to geomembranes that can be suitably softened by a solvent, restricting chemical welding to PVC and Urethane-based geomembranes. An advantage of chemical welding is its ease of application, requiring only a little more than a paintbrush and the appropriate solvent. Despite the ease of use, chemical welding is hugely subject to environmental conditions. Low temperatures or high humidity can significantly affect the quality of a chemical weld.
Wedge-Welding
Wedge welders are smaller hand-held machines that weld two overlapped sheets of materials. There are two types of wedge welders, single-wedge and split-wedge (see images below). The single-wedge welder heats the interface between the two materials with a heated metal “wedge,” Then rollers immediately press the materials together to form a weld. The thermoplastic materials become fused at a molecular level. A split wedge is used on thicker geomembrane grades to create an air channel down the middle of the weld. The integrity of the weld can then be tested by pressurizing the channel with air to ensure an air-tight, and therefore liquid-tight weld has been created.
Layfield uses wedge welding as the basic technique for welding both prefabricated liners in our shop and liner installations in the field. Wedge welders run comparatively high speed between clean, overlapped material and are used for their long straight welds. More complicated work, such as curves or attaching pipe boots, should be avoided with a wedge welder; detailed work like this requires hot-air, extrusion, or chemical welding.
Many geomembrane installations require our crews to utilize several different welding techniques on the same project. Layfield Installation Technicians are fully trained in all geomembrane installation and testing aspects for primary and secondary containment applications. Our Quality Assurance/ Quality Control documentation is available for all projects, which thoroughly details and logs our geomembrane installation, welding, and testing procedures.
To learn more about Layfield Geomembrane Liners – click here.
Related Articles
View All News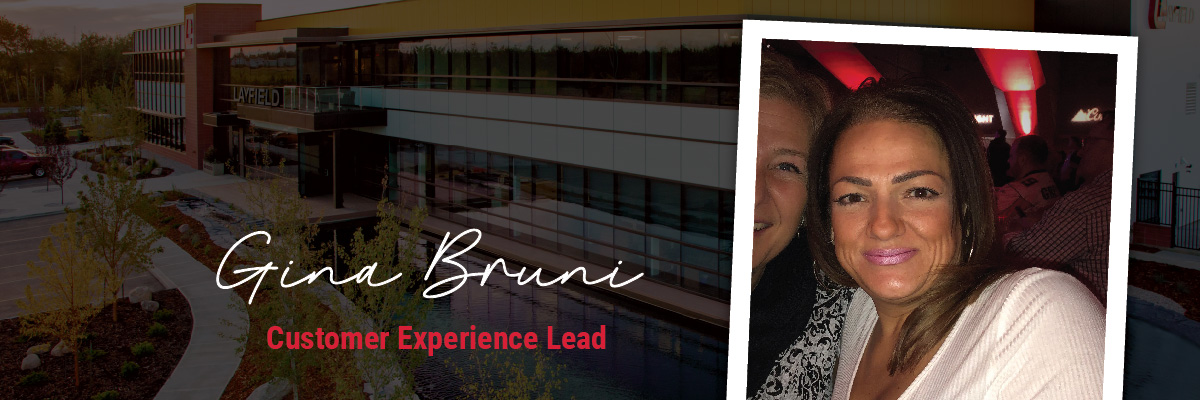
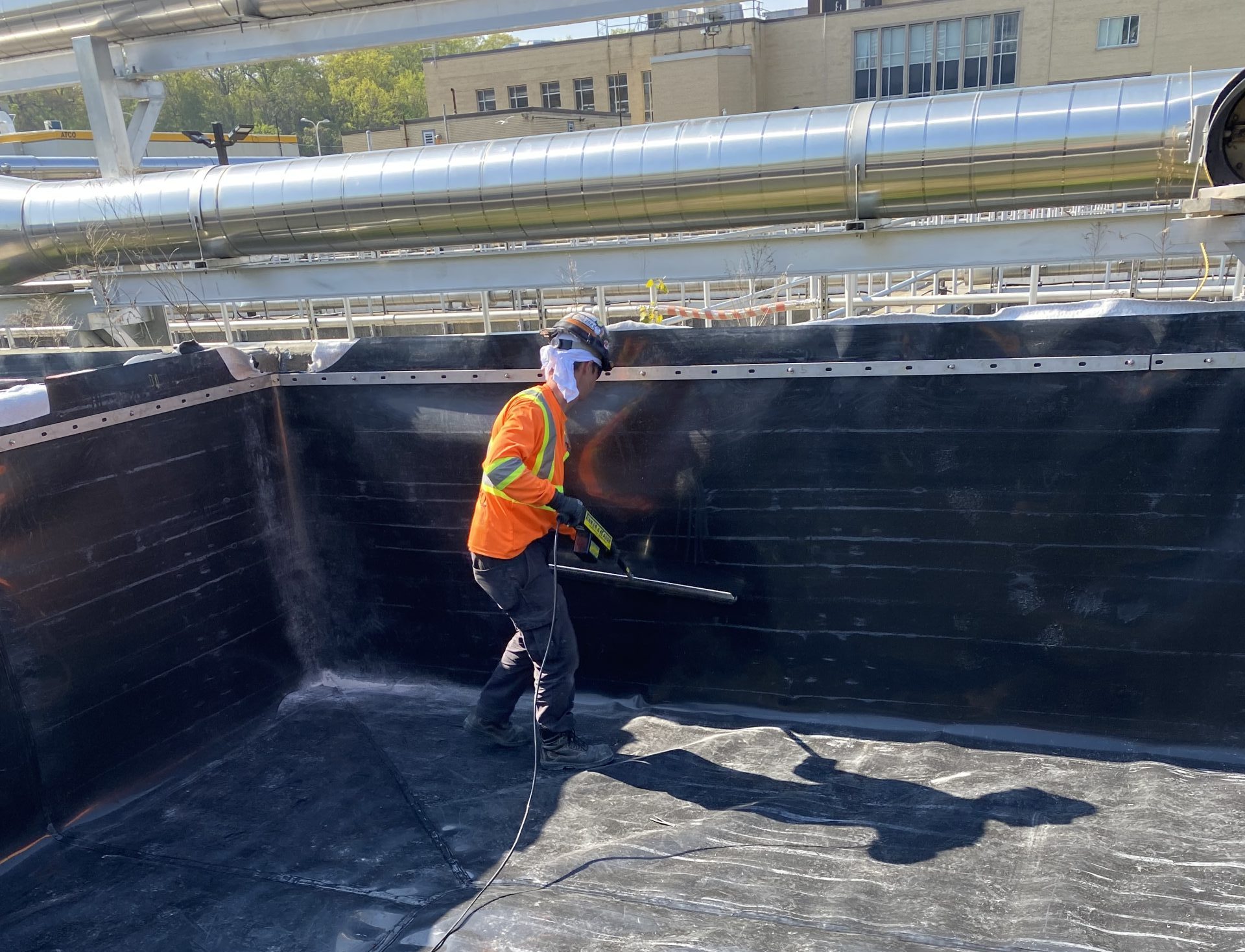
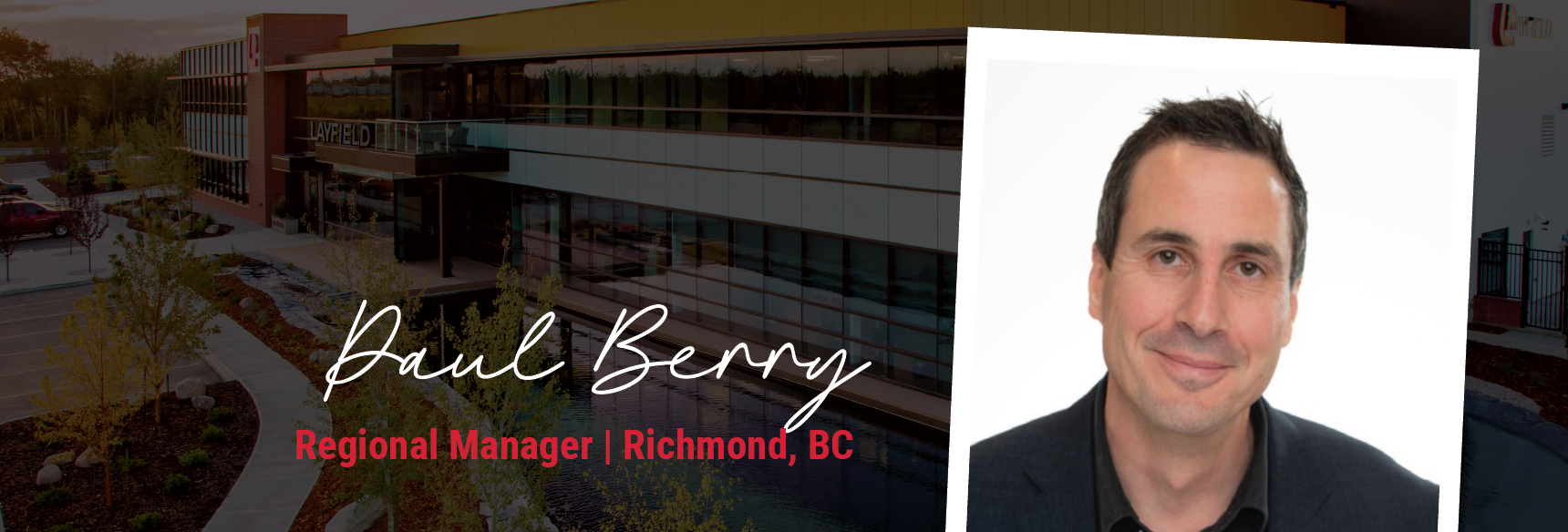
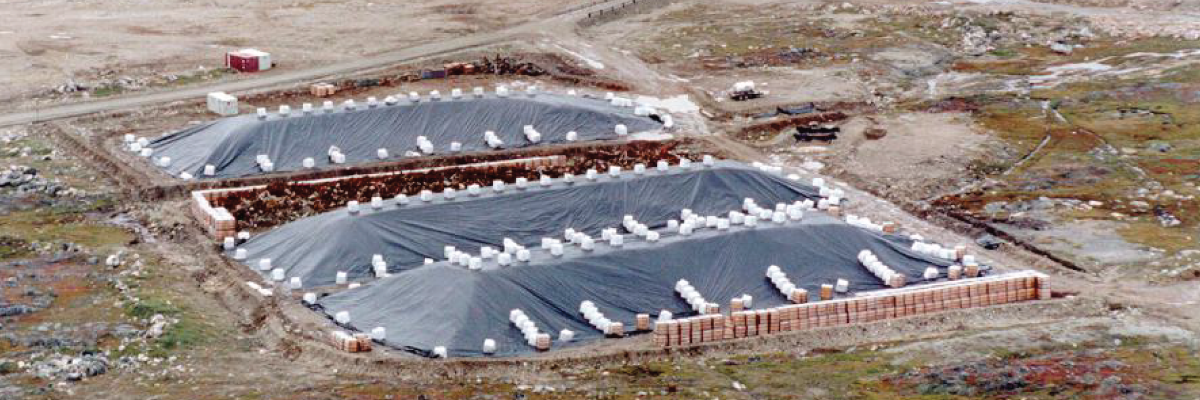
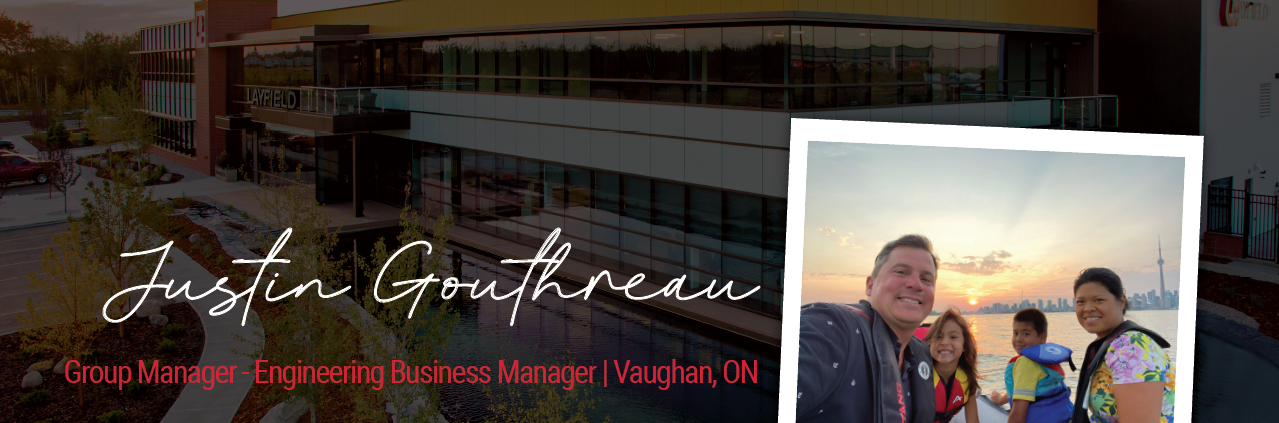

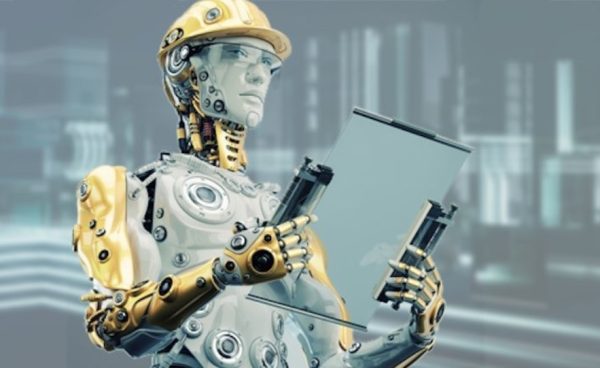
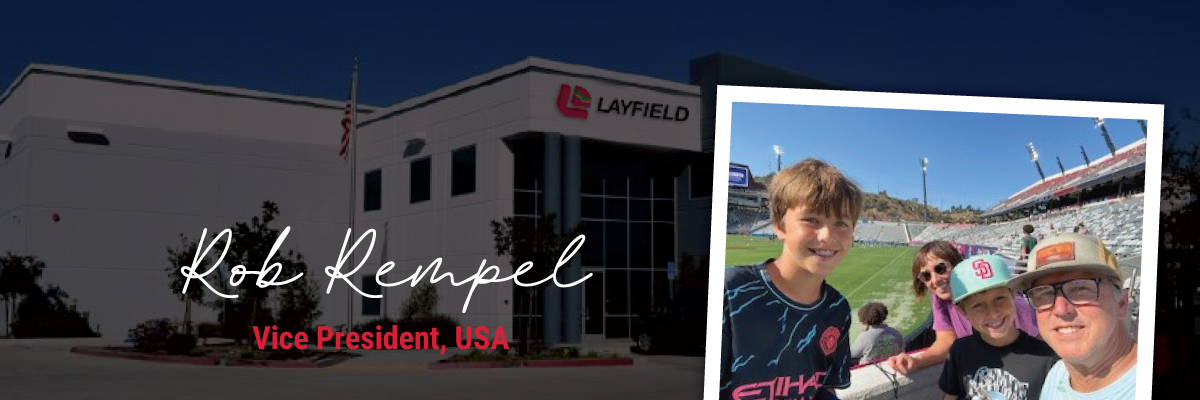
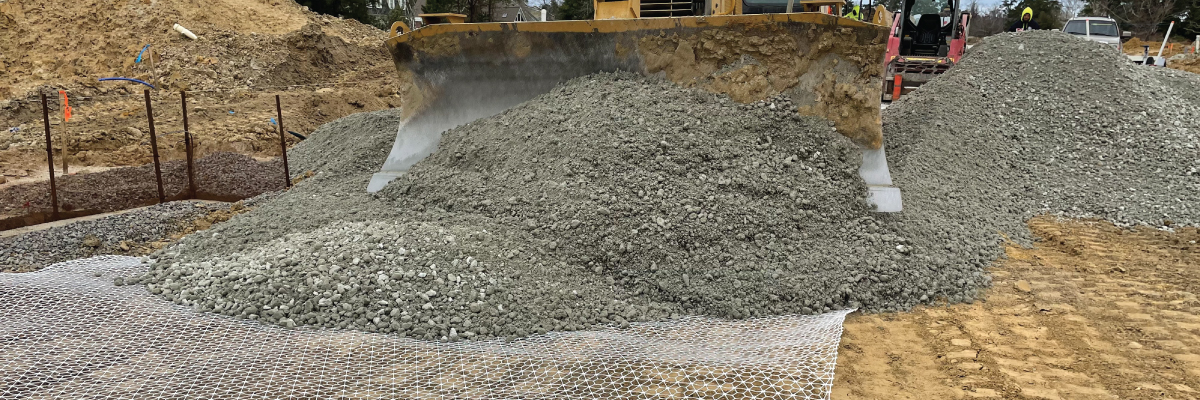
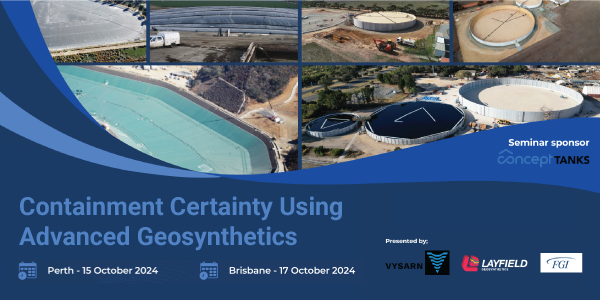